Follow Procedures Training Launched: Now Your Work Begins
FAA just posted the “The Buck Stops Here” web-based training on the human factors website. A website training system, alone, will hardly impact the No. 1 challenge in aviation maintenance: the design and adherence to technical procedures. The new training merely offers a vehicle to increase attention to procedural compliance. Now, you have another tool to address procedural noncompliance. Dr. Bill offers a few implementation ideas for your consideration.
Background
For the past few years, the FAA Maintenance Human Factors research team, mostly at the FAA Oklahoma City Civil Aerospace Medical Institute, has been revisiting the challenges associated procedural compliance in aircraft maintenance. It is not a new topic. It is a continuing challenge that affects every aspect of aviation. The issues/questions seem straightforward. Why is it so difficult to follow procedures? Why does procedural noncompliance remain as a significant contributing factor in most negative events in aviation maintenance? What actions can alleviate the challenge?
In the January/February 2018 issue of Aircraft Maintenance Technology Johnson described some of the empirical work that was the basis for the new web-based Follow Procedures training. The team conducted about 175 90-minute interviews with AMTs, supervisors, and those who wrote maintenance procedures. The interview topics were based on an extensive review of NTSB procedure-related accident reports and on hundreds of voluntary submissions from the NASA Aviation Safety Reporting System. The interviewers asked mechanics to tell stories about negative events where procedures were not followed. A combination of the accident documents, the voluntary reports, and interview stories help define the training. The important finding was that procedural noncompliance was not from a lack of knowledge but from an industry culture of completing perceived safe and quality work as quickly as possible. Thus, the research team surmised that the best way to address the procedural noncompliance was to address the culture. The rest of this article talks about the training and what individuals and organizations can do to address the challenge.
The Follow Procedures Training Described
The 45-minute web-based training program, with all files, can be downloaded from the training section of www.humanfactorsinfo.com. The web-based training module also runs from the FAAST website (www.FAASafety.gov, free registration required). We recommend the FAAST site since it includes a post-training exam and it issues a completion certificate. Early users have already given the training good reviews.
The training is a multimedia mix with animations and short quizzes along the way. There is audio for selected portions of the training. To keep things moving at the user’s pace, some of the materials require reading. Figure 1 shows a screen from the training that presents key attributes: Safety Champion. The training reinforces these champion attributes.
At the end of the training, learners are strongly encouraged to download and use the before and after checklists. There are different sets specifically designed for mechanics, managers, or procedure writers. Figure 2 shows the job cards for managers. The training ends by asking users to sign a “Safety Pledge,” shown in Figure 3, to be a champion of an improved workplace culture of following procedures.
Again, the training is a start but it must be only one part of the campaign to change the culture of procedural compliance. What should you do now?
Actions for Government, Organizations, and Individuals
FAA Action
Government research usually does an excellent job with research and development. Government scientists/engineers/psychologists are great at collecting data. They usually validate the data by talking to workers/citizens, and then write detailed research technical reports. In many cases the research results in development of guidance materials and/or software tools. The FAA Maintenance Human Factors website (https://www.faa.gov/about/initiatives/maintenance_hf/) contains many such reports, advisory documents, software, media, and training support materials.
Government, because of funding design and the regulatory mission priority, often drops the ball when it comes to fielding and supporting the research projects. Commercially that includes marketing, sales, product support, and customer service. These activities are seldom the forte of government. The new web-based follow procedures training must be supported by government! This article and promotion by the FAA Safety Team, are example steps in product promotion and support direction.
The timing is right for customer support of the procedural compliance training initiative. FAA oversight, over the past few years, has changed from a policy of strict administrative enforcement to one of applying cooperative measures to achieve increased safety and regulatory compliance. When individuals or organizations must respond to an FAA discovery of procedural noncompliance, the new training imitative, with supporting activity, can be an ideal suggestion to address the issue. Propose to change the culture of procedural noncompliance with the FAA web-based training as a key component of the potential cultural change. Your FAA inspectors are likely to see the value and accept the training as a way to improve procedural compliance. FAA inspectors have “walked the walk” of being mechanics. They can offer other ways to help increase procedural compliance.
Organizational Action
Organizational action is critical when it comes to affecting culture change. Everyone must buy in to change. Top executives must demonstrate the commitment to procedural compliance in words and actions. And recognize that 100 percent compliance may take a bit more time. It is also likely to reduce delays from rework. It will reduce expensive errors and worker injury. Leaders must accept the tradeoffs. The executive must convince middle managers that increased procedural compliance is a renewed top priority. Selected organizational performance measures must be cognizant of all issues associated with 100 percent procedural compliance. Higher compliance assurance must have similar value to high on-time departure and other reliability rates. Procedural compliance must be important on the list of key performance indicators. It can renew the commitment to the corporate fiduciary responsibility to flight safety of customers.
Strong words from the top can set the general tone, but actions from middle management have greater impact on the daily maintenance work. Continuing safety and low error rates must not be a justification for past procedural noncompliance (“past sins”). Workers must be encouraged, every day, that 100 percent procedural compliance is the goal. Procedures that are unnecessary, complicated, incorrect, incomplete, or unavailable must be documented and addressed, prior to continued work. This action will help correct or eliminate poor procedures, thus raising compliance.
What are immediate actions to accompany the training?
1. Written statement from top management that the organization is recommitting to 100 percent procedural compliance. Management recognizes that this is team effort.
2. Written statement of commitment from labor leaders, in support of management letter.
3. Written statement from Engineering Department committing to rapid response to mechanic recommendations regarding problematic procedures and/or procedure use issues.
4. Statement from local FAA inspection team that they will assist/cooperate with renewed commitment to 100 percent procedural compliance.
5. Personal individual commitment from every person in the organization to champion the culture of 100 percent procedural adherence.
6. Use shift meetings to launch and reinforce the Follow Procedures training.
7. Consider paying an incentive to every worker that submits a training completion certificate from the FAA website.
8. Distribute the Before and After Procedure Following job cards (Available from training program or FAAST representative).
Individual Commitment and Action
Workers must commit to become champions of the procedural compliance culture. That means that workers must be not only introspective of their own behavior but also apply appropriate peer pressure. Remember that every time a procedure is not followed, and there is no immediate safety consequence, it is positive reinforcement to not follow the procedures. That must end!
Workers should engage with the Follow Procedures training in a serious way. Use the 45 minutes of training to question your own work behaviors and to recommit to 100 percent procedural compliance. Such behavior is beneficial to the aircraft, passengers, the organization, and to worker health and safety. Full procedural compliance will be achieved only when workers take individual personal and professional satisfaction with the knowledge that they followed procedures 100 percent.
The Bottom Line
The very start of the training uses the graphic in Figure 4. It explains that: “Everyone is part of the procedural compliance challenge. Therefore, everyone is part of the solution.”
Enough said.
About the Author
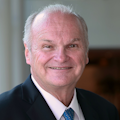
Dr. Bill Johnson
Chief Scientific and Technical Advisor Human Factors in Aviation Maintenance, FAA
““Dr. Bill” Johnson is a familiar name and face to many industry and government aviation audiences. Johnson has been an aviator for over 50 years. He is a pilot, mechanic, scientist/engineer, college professor, and senior executive during his career. That includes 16+ years as the FAA Chief Scientific and Technical Advisor for Human Factors.
Dr. Bill has delivered more than 400 Human Factors speeches and classes in over 50 countries. He has 500 + publications, videos, and other media that serve as the basis for human factors training throughout the world.
Recent significant awards include: The FAA “Charles E. Taylor Master Mechanic” (2020); The Flight Safety Foundation - Airbus “Human Factors in Aviation Safety Award” (2018), and the International Federation of Airworthiness “Sir Francis Whittle Award” (2017).
Starting in 2021 Johnson formed Drbillj.com LLC. In this new venture he continues to bring decades of human factors experience to aviators, worldwide.