Proper Methods for PCA Maintenance
To maintain comfortable temperatures in a parked aircraft, a pre-conditioned air (PCA) unit is connected to the aircraft while at a boarding gate or maintenance location. The passenger boarding experience is enhanced with good cabin air quality, and modern aircraft contain sensitive electrical components that require a temperate environment.
Maintenance functions may require “normal” room temperatures for successful results. On-board systems require protection against freezing or excessive heat. There are electrically powered fixed mounted PCAs and engine-generator powered mobile units. This column will cover the topics of refrigeration, airflow and electrical aspects of PCAs.
Preventive maintenance is an essential part of ownership and/or maintenance of pre-conditioned air units. Maintenance tasks and intervals are specified by the equipment manufacturers and published in their maintenance manuals. Some airlines/airport maintenance departments and maintenance contractors write their own preventive maintenance tasks and intervals. However, the manufacturer’s suggestions should be considered the minimum standard. It’s OK to perform additional steps but never fewer.
Let’s take a look at some common PCA maintenance tasks and the purposes of the procedures.
Lock Out Tag Out (LOTO)
The Occupational Safety and Health Administration (OSHA) standards for control of hazardous energy sources should be followed as part of preventive maintenance activity. The first maintenance task should advise to lock and tag the (switched off) disconnect source. The main power will need to be “on” for operational testing purposes later. However, all panels and doors should be in place for that activity. It’s a good idea to quickly run equipment prior to preventive maintenance procedures to verify the machine works correctly.
Filters
The airport ramp can be a dirty environment. Cleaning or changing filters is an elementary task, but it remains an important one. In order to heat or cool air efficiently, the mass air flow needs to be as specified by the equipment’s design engineers. Dirty filters can affect the amount of air getting to the cooling and heating components, and ultimately, the aircraft cabin.
Intervals for cleaning or changing filters will be according to manufacturer recommendations. Filter types, sizes and efficiencies vary among brands.
PCA filters are generally washable or replaceable. Washable filters will get cleaned at quarterly intervals, unless local environmental conditions dictate otherwise. A good way to clean washable filters is to fill a wash tub with a warm water/dishwashing soap mix. Agitate the washable filters in the tub to flush out contaminants. If there is a lot of pollen or large particles on the filter surface, vacuum this off first. Rinse the filters with fresh water and set them in fresh air to dry. Sunlight is a wonderful disinfectant so direct sun is preferred for drying.
Replaceable filters get replaced per manufacturer recommendation. Some modern PCAs can monitor filter pressure drop and can alert on a human interface display when it’s time to change filters.
Evaporator Coil Cleaning
The evaporator is the component where the cold air is made, so to speak. It is where heat is transferred out of the ambient air and into the refrigerant flowing within the evaporator fins and tubes. This isn’t meant to be a Refrigeration 101 lesson, so simply understand the evaporator needs to be clean for proper heat transfer.
The best way to keep an evaporator clean is to never let it get dirty. With proper filter maintenance, personnel shouldn’t need to worry too much about the evaporator. Evaporators aren’t very easily accessed in many PCA brands as they are trapped inside a sheet metal plenum. If troubleshooting indicates a dirty evaporate may be an issue, consult the manufacturer.
When cleaning an evaporator, a plain water rinse is usually all that is needed. Very mild chemicals, meant for evaporator cleaning, can be used if there are substantial contaminants on the evaporator fins. Cabin supply air flows through the evaporator, so strong chemical cleaning should not be performed.
Heating Elements
Heating functions get verified before each heating season. Electric elements can be verified using an ammeter and specified circuit current values. A thermometer is used to verify heating discharge temperature. Consult the manufacturer for heating element cleaning procedures, if applicable. Year-round heating regions may require additional checks.
Condensation Pumps
Some PCAs utilize a pump to remove evaporator condensation from the plenum. Sometimes the water is pumped right to the ground beneath the PCA and sometimes local code requires pumping to a sanitary drain. Be certain the pump is working as designed. Check with the PCA manufacturer for suggested condensation pump winter “layup” procedures. The pump is checked before cooling season start-up. Year-round cooling regions may require additional checks.
Condenser Coil Cleaning
Short of a refrigeration process explanation, understand that the condenser is an integral part of the refrigeration system and will not function efficiently (or at all) if very dirty. Even a thin layer of oily residue can hinder heat transfer and harm efficient cooling operations.
Sometimes a plain water rinse is enough for cleaning a condenser coil. Condensers at an airport get contaminated with exhaust from aircraft and ground support equipment and may require chemical cleaning. It is advised to consult the PCA manufacturer (and/or coil manufacturer) for the appropriate condenser coil cleaner to be used.
There are unique materials used by individual coil manufacturers. Various protective coil coating products are employed. This requires a coil manufacturer consultation to determine what cleaning chemicals are best for their coils. Unauthorized cleaning products can damage the condenser and make its operation worse. Chemical cleaners get mixed with water, per the chemical manufacturer directions, and applied as directed. Many of these cleaners use a foaming action to drive out contaminants from deep within the coil fins or channels. Consult the manufacturer to determine if using warm water can improve this process. Be certain to rinse off the chemical completely and only leave it on for the recommended amount of time.
When cleaning the condenser coil, also clean the condenser fan blades with a freshwater rinse. Be careful not to spray water directly at bearings or any openings in the condenser fan motor. Some local environmental codes require capture of rinsing water. Condenser cleaning is performed before the cooling season. In a year-round cooling region, or in an exceptionally dirty environment, more cleanings may be advised. Consult the equipment manufacturer and use their recommendations as the minimum standard.
Electrical Integrity
Visually inspect all electrical components, conductors and terminations for anomalies such as discoloration, insulation heat damage, stray wire strands (whiskers), etc. Termination lug /screw tightening should only be performed with a torque screwdriver or wrench, and only by a qualified electrical technician. Consult the equipment manufacturer literature for proper torque values.
Thermal imaging, by a qualified thermographer, can be useful and is conducted with power “on” while under load. Hot spots found, via thermal imaging, can help find possible electrical issues needing correction before a breakdown occurs. Voltage drop testing, along with voltage and current balance testing, is helpful to assess the integrity of certain components such as contactors and motor starters.
Megohmmeter testing can be beneficial to assess compressor health. Some of these checks are for a seasoned HVAC technician. However, a visual inspection by semi-qualified personnel can catch something obvious needing further evaluation. Verify condition of VFD cooling fans and filters. Check the compressor crank case heaters, if installed. Crank case heaters keep the oil in the compressor warm during “off” cycles. Refrigerant will migrate to the cold compressor and condense during “off” periods. This liquid refrigerant will rapidly vaporize upon the next compressor start. Oil gets pushed out of the crank case and into the compressor discharge pipe with the rapidly boiling refrigerant. This is called oil carryover.
When the compressor is running in a poorly lubricated condition, metal on metal wear is taking place. This leads to compressor failure. A qualified technician can check operation of the crank case heater with an ammeter. The semi-qualified technician can check the crank case for being warm to the touch during off cycles. Electrical Integrity is checked semi-annually.
Mechanical Integrity
As for mechanical integrity, ensure that fasteners are secure and torqued. Check PCA mounting to the boarding bridge or stand. Check blower and motor mounting, shaft, coupling, bearings and blower wheel condition. Lubricate blower bearings per factory recommendations. Check compressor mounts and refrigeration piping brackets. Be sure all mechanical components are secure. Do all this semi-annually.
General Cleaning
Overall machine cleanliness gives an appearance of a competent maintenance program. It’s nice to see clean equipment in great working condition. A clean PCA helps pinpoint a possible refrigerant leak when oily residue is noticed on otherwise clean surfaces. Compressors, motors and frequency drive units without dirt, oil and dust contamination will run cooler and more efficiently. It gives a professional appearance when equipment is left as clean as possible. Clean the unit semi-annually.
Hoses and Aircraft Connectors
Hoses should be visually inspected for internal and external tears, bad connection cuffs (Velcro/zippers), exposed reinforcement rods, etc. Every hole or tear represents lost airflow. Old hoses that end up getting wet inside through the normal condensation process can support organic contaminants.
Look for excessive discoloration and musty smells inside and outside the hose. Replace all old and compromised hoses. Check the aircraft connector for proper latch operation and overall condition. Pay special attention to connector seal integrity. Be sure the hose clamps at the PCA outlet collar are tight. Check hose baskets and reels. Do all of this semi-annually.
Operational Checks
A technician with a fundamental understanding of how PCAs operate can verify machine function and sequence of events during an evaluation. Airflow and refrigeration testing require instrumentation and training to properly obtain and interpret results. Tools such as manometers, digital thermometers, anemometers, refrigeration gauges and electrical multi meters are used to determine proper PCA function by qualified HVACR techs.
Many newer refrigerants don’t have a single point saturation-temperature-to-pressure relationship. Liquid line refrigerant sight glasses are not a good indicator of proper charge as the presence of bubbles may be normal with blended refrigerants. The moisture indicator in the glass, however, should be observed to verify dry system refrigerant and oil. During an operational check, a semi-skilled technician can listen for any “out of ordinary” noises and watch for abnormal vibrations. Be aware of any component short cycling and irregular operations. Semi-skilled technicians can check the supply air temperature with a calibrated thermometer and compare against factory specifications for the ambient conditions. They can also ensure hoses are of proper lengths to eliminate kinks.
HVACR and PCA training should be mandatory for technicians working on these complicated systems. Perform operational check semi-annually.
Conclusion
A temperate aircraft cabin is necessary for a variety of reasons. Always use the factory suggested maintenance tasks and intervals as a minimum standard. Technicians with advanced HVACR skills may wish to go beyond factory minimum maintenance recommendations.
Cleaning and/or replacing filters is one of the most important things a technician can do regarding PCA maintenance. Keeping evaporator and condenser coils clean is also a very important aspect as these components are designed to transfer heat and they perform better when clean.
Electrical checks are important for human as well as machine health and safety. Equipment mechanical components should be evaluated, and hardware tightened to specification.
Hose and connector condition, though often overlooked, is extremely important for proper PCA operations. Clean, leak-free hoses support good cabin air quality.
A final operational evaluation and discharge air temperature check can verify satisfactory operations. Aircraft need to be supplied with adequate air volume and temperature while on the ground. A well maintained PCA will provide these needs.
Tim Fox is a facilities engineering and maintenance projects and programs manager at United Airlines. He has been employed at United Airlines for 32 years and has been an HVACR practitioner for 36 years. He serves as United Airlines’ subject matter expert for aircraft preconditioned air equipment and facility HVACR matters. He can be reached at [email protected]
About the Author
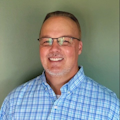
Tim Fox
Tim Fox is a facilities engineering and maintenance projects and programs manager at United Airlines. He has been employed at United Airlines for 33 years and has been an HVACR practitioner for 37 years. He serves as United Airlines’ subject matter expert for aircraft pre-conditioned air equipment and facility HVACR matters. He can be reached at [email protected].