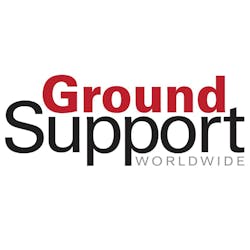
Across many industries, including aviation, the active workforce and incoming labor pool were drastically affected by the COVID-19 pandemic. Today, businesses around the globe are still working to recruit people to fill job vacancies.
Within the aviation industry, ground support-focused companies are working through personnel challenges on a daily basis.
In the Ground Support Worldwide 2023 State of the Industry survey, readers identified finding and retaining staff as the greatest challenge to their businesses.
The next greatest challenge highlighted by businesses was acquiring and maintaining equipment.
These two trending issues paint a unique picture of the challenges being faced by ground support equipment (GSE) maintenance providers.
Personnel Challenges
The number of mechanics in the labor pool have decreased, according to Chris Schaeffer, vice president of GSE at GAT Airline Ground Support. What’s more, he notes the experience of those GSE technicians in the labor pool varies greatly.
“They are either high quality or very new to the trade,” Schaeffer says. “The high-quality mechanics are looking for higher pay and getting it as is the rule of supply and demand.”
The reduced number of veteran GSE mechanics and technicians can be attributed in part to the pandemic’s impact on experienced personnel.
“I found mechanics who had years of experience planning to retire in a few years bumped up that timetable post-pandemic,” says Schaeffer. “That took away those years of helping mentor less-experienced techs.”
Finding and retaining maintenance personnel for the GSE space requires meeting specific criteria both of job seekers and GSE maintenance providers.
“Mechanics with an industrial background understand urgency, can follow a repair manual and are usually good at documenting,” Schaeffer notes. “Many of my applicants are heavy duty truck mechanics that want to change into something where they are more appreciated with regular and steady hours for a work-life balance.”
Finding a solution to personnel shortages requires a case-by-case approach. According to Schaeffer, finding talented candidates to fill vacant roles is critical. But perhaps more importantly, finding employees who want to learn and grow within the industry can pay huge dividends.
New-hires who wish to learn a skill can start with smaller tasks and then build their knowledge of the industry. While newcomers are assigned less skilled tasks, veteran technicians can be freed up to do repairs that require more experience and training and offer mentorship to team members.
Working as a team, with leaders who value their fellow colleagues, is crucial to keeping mechanics engaged in the GSE industry.
“People can be anywhere to earn a living, but they choose to be here, with you. I make a genuine effort to create an environment of appreciation and respect,” Schaeffer says. “Appreciation is in the form of pay, but also seeing mechanics not as a commodity but as tradesmen with years of practice on their craft.”
Evolving Maintenance
As GSE maintenance shops continue to recruit the workforce, it is important to consider the types of maintenance tasks that will be performed.
The increased use of electric vehicles (EVs) and a push for more electric ground support equipment (eGSE) across the industry is changing the scope of maintenance required.
eGSE, Schaeffer notes, has far less fluids and filter changes, fewer components to fail, and an easier-to-diagnose drivetrain.
“I’ve personally and professionally been involved in EVs for a decade and can say they are easier to diagnose,” he says, adding that EVs have less downtime and are more robust than their non-electric counterparts.
GSE, in general, is being engineered to require less maintenance and upkeep, according to Gerry Hoadley, director of ground support equipment at Waev Inc.
He notes that routine maintenance is greatly reduced on GSE powered by lithium-ion (Li-ion) batteries, which reduces associated costs.
“This cost reduction stems from many factors,” he says.
According to Hoadley, they include a minimal number of moving parts within the drive system, regenerative braking lessening brake pad wear, and battery chemistry that requires no serviceable cooling or heating system.
The batteries themselves require zero maintenance, he adds.
“They also allow for opportunity charging – charge them anytime, for any duration to partially charge or top-off without negatively impacting the battery – eliminating inconvenient charging parameters,” he says. “Li-ion batteries also don’t require posts to be cleaned or fluid to be monitored or added, making them much more reliable.”
“Lithium batteries like to be at a state of 20-80 percent state of charge (SOC), and about 100 degrees Fahrenheit,” Schaeffer points out. “Plus, they don’t need periodic watering like lead acid, nor to be unplugged after charging.
“Keeping 20-80 percent SOC is relatively easy with battery management and has the biggest impact on the expected life of the battery,” he continues. “The battery temperature is a factor, but in my opinion, not enough to warrant liquid cooling. Liquid cooling adds cost, complexity and maintenance for little return on investment.”
As equipment evolves and fewer maintenance requirements are engineered into GSE, requirements for maintenance personnel will also change.
“I predict in the next few years, as electric is more accepted and embraced, the need for mechanics will decrease,” Schaeffer says. “I also predict the level of training and experience needed will also decrease. The mechanics coming from a 2–4-year program at a trade school will be more effective repairing electric than fluid fuel when they first enter the workforce.”
About the Author
Josh Smith
Editor
Josh Smith served as editor of Ground Support Worldwide as editor from 2016 through 2024. He oversaw production of the print magazine, created GSW's newsletters on a daily basis, and updated the latest news on AviationPros.com.