Fork Truck Safety is a Core Value for Ground Support and Material Handling
Ground handling operations at airports around the world – particularly cargo handling, use powered industrial trucks (PITs – forklifts / fork trucks) in warehouses, cargo facilities and many other areas. These are used in the course of operations, and are valuable for the movement of cargo, equipment and materials in preparation for transport.
However, every year, thousands of workplace incidents, injuries and fatalities related to powered industrial trucks occur. Fatality statistics indicate the three most common fork truck fatalities involve fork truck overturns, workers being struck by, and workers falling from fork trucks. The fork truck, the environment (e.g., warehouse, factory, tarmac, driving surface, ramp, dock) and operator actions can all contribute to fatalities, injuries and property damage involving fork trucks.
Incidents can involve property damage, including damage to overhead sprinklers, racking, pipes, walls, floors, loading platforms, electrical conduits, other vehicles and machinery. Unfortunately, most of these can be attributed to a lack of safe operating procedures, lack of enforcing safe operation and insufficient or inadequate training.
The Occupational Safety and Health Administration (OSHA) Powered Industrial Trucks standard “contains safety requirements relating to fire protection, design, maintenance and use of fork trucks, platform lift trucks, motorized hand trucks, tractors and other specialized industrial trucks powered by electric motors or internal combustion engines”[1]. Operator training requirements apply to all industries where powered industrial trucks are being used (except agricultural operations).
History of Forklift/PIT Standards and Requirements
OSHA revised its existing standard and requirements[2] for powered industrial truck operator training in 1999. The new provisions were intended to reduce the number of injuries and deaths that occur as a result of inadequate operator training. They apply to all industries -- including general industry, construction, shipyards, marine terminals and longshoring operations -- in which the trucks are used, except agricultural operations.
These provisions mandate a training program that bases the amount and type of training required on the operator's prior knowledge and skill; the types of powered industrial trucks the operator will operate in the workplace; the workplace hazards present; and the operator's demonstrated ability to operate a powered industrial truck safely.
It also requires refresher training if - the operator is involved in an accident or a near-miss incident; the operator was observed operating the vehicle in an unsafe manner; the operator has been determined during an evaluation to need additional training; there are changes in the workplace that could affect safe operation of the truck; or the operator is assigned to operate a different type of truck. Evaluation of each operator's performance is required as part of their initial and refresher training, and at least once every three years.
Employee Training
It is critical that every employer develop, implement and enforce a comprehensive documented PIT safety program that includes operator training, evaluation, licensure and a timetable for reviewing and revising the program.
At minimum, PIT programs should ensure that workers do not operate a fork truck unless they have been trained, evaluated and licensed, and that licenses are required for every type of vehicle the employee will operate.
Training must cover all aspects of the equipment the worker is going to operate including the basics (e.g. when to set the parking brake) and factors that affect the stability of a fork truck—such as driving behavior, the weight and symmetry of the load, the speed at which the fork truck is traveling, the operating surface, tire pressure and type of tire, and how to perform a daily operational inspection per manufacturers (or your company) requirements. Operators must understand handling asymmetrical loads when their work includes this activity. Operators of sit-down type fork trucks must understand the overhead guard is present to protect them from material being moved from an overhead position or debris from their load falling on them.
It is critical to ensure fork truck operator restraint systems are always used. Since 1992, fork truck manufacturers have been required to equip new sit-down type fork trucks (counterbalance) with operator restraint systems. Many manufacturers offer restraint systems that can be retrofitted on older fork trucks. Many operator fatalities might have been prevented if the operator had been restrained. Train the operator to stay on the truck and hold firmly onto the steering wheel and lean away from the point of impact if lateral or longitudinal tip over occurs. The overhead guard and the structure of the fork truck can crush the operator's head, limbs or torso if he or she falls or jumps out the operator's compartment during a tip-over.
Train operators of stand-up style fork trucks with rear access that when a stand-up rider truck tips over, they can exit the vehicle by simply stepping backward, perpendicular to the direction of the vehicle's fall, to avoid being crushed. In this situation, the operator usually should attempt to jump clear of the vehicle, and should be trained accordingly.[3]
On numerous occasions, fork truck operators have stated - without reserve - their opinion of “what a nuisance the restraint system is and their dislike for it.” My response was always positive, but to reinforce and emphasize the legal, company and operator requirements for their position. A seatbelt is designed to keep the worker inside the protective envelope of the operator’s compartment in case of an accident, so there is no negotiating regarding seatbelt use and operator safety.
At our former employer (a Fortune 100 Company), training included eight hours of classroom and interactive training, after which a written test with a minimum passing score was administered. A minimum of eight hours of hands-on driving for each vehicle along with a trainer under working conditions was required with a final review and evaluation. Finally, the driver was on probation and observation by supervision for a period of 60 days.
Fork Truck Inspection and Maintenance
Fleet managers and operations supervisors should establish a vehicle inspection and maintenance program. Every manufacturer has recommendations for upkeep, performance and inspections (daily, monthly, quarterly, annual), but from our experience, fork trucks should be inspected by the driver at the beginning of each shift. If not done at the beginning of the shift, at a bare minimum, they should be inspected daily, if the equipment is used around the clock.
Operators should check for any visible defects, including checking the tires, forks, seat belts, brakes, warning devices and fluid levels. An operator on a previous shift might not want to admit that they ran into something or were involved in an incident.
If Lifting Personnel – NOT Materials
Ensure only an approved lifting cage is used and is inspected. Adhere to required safety practices for elevating personnel with a fork truck. Also, the platform must be secured to the lifting carriage or forks per the manufacturer’s instructions. Ideally, the platform should be surrounded by steel mesh and approved platform rails, have a secure locking mechanism and for additional safety, should be chained and locked to the lifting carriage or forks.
When lifting people versus loads, always provide a means for personnel on the platform to communicate with the fork truck operator and have shut-off power to the truck whenever the truck is equipped with vertical only or vertical and horizontal controls for lifting.
Working Around Pedestrians
While possibly unavoidable, separate fork truck and pedestrian traffic wherever possible. This can be done – if possible – by limiting some aisles to workers on foot only or fork trucks only, designated travel lanes in aisles, and avoid storing bulk materials and equipment in aisles where combined traffic exists. Fork truck use should be restricted near time clocks, break rooms, cafeterias and main exits, particularly when the flow of workers on foot is at a peak (such as shift end, lunch, or during breaks).
Install physical barriers (bollards, guardrails) where practical to ensure that workstations and congested work areas are isolated from aisles with heavy fork truck traffic. Evaluate intersections and blind corners to determine whether overhead dome (parabolic) mirrors could improve the visibility of blind spots for fork truck operators and workers on foot.
And finally, make the effort to alert workers when a fork truck is nearby. Use horns, audible backup alarms and flashing lights to warn workers and other fork truck operators in the area especially around blind intersections, obstacles and office area exits and entrances. Flashing lights over doors can be important in areas where the ambient noises levels are high.
The higher the volume of personnel in an area shared by fork truck traffic, the greater the risk of an accident, regardless of how diligent the efforts are to keep everyone safe. I recall an incident where an office area had to be situated adjacent to a main aisle, but the offices entrances were recessed into alcoves separating them from the traffic lanes with flashing lights installed above the alcoves on the outside wall indicating when the office doors were opened to alert nearby fork trucks. Regardless of these measures, one day an employee came running out of the office so fast without paying attention to their surroundings that they ran headfirst into a fork truck that stopped for the flashing light even though the operator had stopped. In any location where sudden movement or inattention to surroundings may pose a hazard, the potential of those hazards has to be reinforced to everyone.
The Work Environment
Ensure that workplace inspections are routinely conducted by an individual who can identify potential hazards and conditions that are dangerous to workers and equipment operators alike. In essence, you have to consider anything or anyone that can be exposed to hazards. Hazards include obstructions in the aisle, blind corners and intersections, electrical equipment, building columns and fork truck traffic too close to workers on foot. The person who conducts the inspections should have the authority to take immediate action and implement prompt corrective measures.
Install workstations, control panels, electrical panels and equipment away from aisles whenever possible. Do not store bins, racks, equipment, pallets, or other materials in aisles or at corners, intersections, or other locations that obstruct the view of operators or workers.
Always enforce safe driving practices such as obeying speed limits, stopping at stop signs, moving cautiously in and around intersections (use your horn to alert personnel of your presence at blind spots and when personnel are preoccupied and blocking your travel path).
Just as important is awareness training (pedestrian safety) for all personnel to be aware of fork truck traffic, workplace hazards and to use caution when walking around, near, or approaching a vehicle at all times. Also, it is critical to repair and maintain floors and driving surfaces, repairing cracks, crumbling edges on ramps and other defects on loading docks, aisles and on other operating surfaces.
From the Driver / Operator Viewpoint
“All the training in the world” is not a replacement for hands-on / practical experience on the vehicle. You, as the operator, are “the master of” your own destiny – which cannot be covered in a textbook. Safety is not “common sense,” but respecting your vehicle and your co-workers. Do not rely on anyone else to do what is required for your job (e.g., installing a dock plate, trailer landing gear, wheel chocks or “dock-locks” on trailers, vehicle inspections and reporting problems promptly for correction). Make sure the driver of the transport vehicle understands your requirements for loading and unloading to assure your safety. Also verify the vehicle you are loading will support the weight of your truck and/or the load you are carrying.
Having a semi-trailer roll away from the dock while entering the trailer with a fork truck, and rolling off the trailer onto the dock floor because the driver did not set the air brakes, the chocks were not installed, and the dock plate was set for loading (indicating the vehicle was set for the load) is a life changing experience - even if not seriously injured (yes, even experienced drivers can make assumptions - with negative consequences).
Closing Thoughts
Always remember, workplace safety should not be a “priority” - because priorities can and do change. Your company / workplace safety program should be a core value of your company’s operation and culture.
Safety is not a choice, it’s part of everyone’s job – and it starts with you.
About the Author
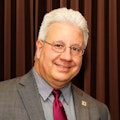
Steven K. Fess
Steven K. Fess is a Certified Industrial Hygienist, Certified Safety Professional, Safety Management Specialist, and an AIHA Fellow. He has 44 years occupational health and safety experience, working at a Fortune 100 for 38 years in R&D, manufacturing, warehousing and logistics, facilities/maintenance operations, and other specialized areas. Semi-retired, he is currently a member of Pine Bluff Environmental Associates, KEMRON Environmental Services’ corporate safety team, and a part-time employee, consultant, trainer, and site safety representative for projects assisting numerous small businesses, consulting firms, and manufacturers.
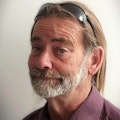
Douglas E. Roemer
Douglas E. Roemer was a professional fork truck driver / material handler / powered equipment trainer and powered equipment instructor for a Fortune 100 company. During his 43-year tenure he operated numerous types and sizes of fork trucks and trained hundreds of employees in environments ranging from warehousing and rack storage to equipment manufacturing with dense employee populations. He is a previous winner of the Xerox Corporation Corporate Fork Truck Rally and the IMMS Rochester, NY Chapter International Fork truck Rally Driving competition, winning numerous awards on counterbalance and narrow-aisle vehicles. His career also included time as a Union Representative (including Sargent-at-Arms, Treasurer and Contract Negotiations team member).