AI in Aviation Line Maintenance: A Strategic Response to Delays, Satisfaction, and Staffing Challenges

In the rapidly evolving aviation industry, the integration of Artificial Intelligence (AI) into line maintenance operations presents a compelling strategy to address some of the most pressing challenges: managing delays, enhancing passenger satisfaction, and navigating the looming shortage of skilled mechanics. For the more than 45,000 flights every day and 2.9 million airline passengers across more than 29 million square miles of airspace in the US alone, the demand for aircraft mechanics is substantially growing with a need for 710,000 highly skilled technicians fulfilling all levels of positions on the apron. The numbers, however, point to an upcoming employee shortage in these key areas over the next decade.
As airlines strive to maintain operational efficiency and high service standards, AI stands out not only as a technological enhancement but also as a critical operational ally that helps to manage potential staff shortages.
AI and Delay Management
Delays due to maintenance issues are among the most frustrating experiences for passengers and one of the costliest problems for airlines. A significant portion of these delays can be attributed to unplanned maintenance events, which AI can help mitigate through predictive maintenance techniques. By analyzing data from aircraft sensors and maintenance logs, AI algorithms can predict potential failures before they result in groundings or delays. This approach enables maintenance teams to proactively address issues during scheduled downtimes rather than reactively in scenarios that lead to operational disruptions.
Predictive maintenance powered by AI transforms line maintenance from a reactive task to a proactive strategy. Sensors equipped throughout aircraft continuously collect data, which AI systems analyze in real time to predict wear and tear on parts. This not only extends the life of aircraft components but also optimizes the maintenance schedule to reduce the likelihood of aircraft being unavailable due to unforeseen repairs.
Enhancing Passenger Satisfaction
Between January 2019 and February 2023, the Department of Transportation’s data shows that 1.6 million flights were delayed. This amounts to 5.8% of all flights. At the same time, passenger satisfaction is closely tied to their experience with flight punctuality and the condition of the aircraft. Here, AI plays a crucial role by ensuring that aircraft are maintained in peak condition, thereby reducing the chances of onboard issues that could impact the passenger experience, such as malfunctioning seats or inoperative entertainment systems. Moreover, AI-driven tools provide maintenance teams with quick diagnostic capabilities, which means issues can be resolved faster and with greater accuracy, minimizing the time aircraft spend on the ground.
Furthermore, AI can improve the communication flow between maintenance teams and customer service departments. Real-time updates on maintenance status powered by AI can be relayed to customer service agents, who in turn can provide accurate updates to passengers. This transparency helps manage passengers' expectations during delays and mitigates frustration, thereby preserving and even enhancing passenger satisfaction during potentially negative situations.
Addressing the Skills Shortage
The aviation industry is facing an imminent shortage of skilled mechanics, a challenge exacerbated by the rapid pace of technological advancements in aircraft design and functionality. AI provides a dual solution to this dilemma. First, it reduces the burden on existing staff by automating routine diagnostic processes and data analysis tasks. This allows skilled technicians to focus more on complex maintenance tasks that require human expertise.
Second, in the future AI can serve as a training facilitator through virtual reality (VR) and augmented reality (AR) platforms. Although these technologies are not developed enough yet to be used in a professional way, the idea is certainly compelling. They can simulate a wide range of scenarios that mechanics might encounter, providing them with valuable hands-on experience in a controlled environment. This aspect of AI is particularly crucial for rapidly training new staff and for updating the skills of existing personnel to keep pace with new technologies and maintenance practices.
Operational Efficiency and Cost Management
Integrating AI into line maintenance also leads to better management of maintenance resources, from spare parts inventory to scheduling of maintenance personnel. AI systems can forecast the need for replacement parts and ensure that they are ordered and delivered just in time, reducing the inventory costs and storage space requirements. Additionally, AI-enhanced scheduling tools ensure that human resources are optimally deployed, based on the most current and predictive maintenance data, thereby avoiding both understaffing and overstaffing.
Future Prospects
Looking ahead, the role of AI in aviation line maintenance is set to expand even further. As airlines continue to collect vast amounts of data, the potential for AI to refine its predictive algorithms improves, which in turn increases the accuracy and timeliness of maintenance predictions. The ongoing development of AI technologies promises not only to enhance operational efficiency but also to pioneer new practices in aircraft maintenance.
The adoption of AI in line maintenance is no longer just an option; it is becoming a necessity for airlines that aim to remain competitive in a challenging global market. By addressing delay management, enhancing passenger satisfaction, and tackling the skilled labor shortage, AI not only supports current operational needs but also strategically positions airlines for future success. In an era where every minute counts, AI in line maintenance offers airlines the precision and efficiency required to soar to new heights.
About the Author
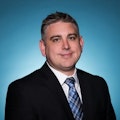
Loren Mathis
Chief Strategic Officer
Loren Mathis is Chief Strategic Officer - Aviation (CSO) at INFORM, a global leader in software development and business process optimization. With over a decade of experience at American Airlines, Mathis brings a wealth of knowledge in operations, resource planning, and technology strategy. A holder of an MBA from the Thunderbird School of Global Management and a Bachelor of Science from Arizona State University, Mathis is poised to steer innovative solutions that cater to the evolving needs of the aviation industry.