Politicians and local press, invited by Rolls-Royce, had a rare chance to experience the FTD (flight training device) for the F-35B Joint Strike Fighter, now officially known as the Lightning II. While our senator and U.S. representative and local press were flying, I was looking for F-35 program folks, “to find stuff out from.”
The F-35B on display was the Marines’ version, the machine with STOVL (Short Take Off, Vertical Landing) capability. The Air Force’s A model (the least-expensive and most-popular) uses conventional runways, and the Navy’s C model sports a tailhook and an 8-foot longer wingspan, as its most-obvious distinctions.
The plane is touted as “the world’s only multi-use fifth-generation fighter,” and has air capabilities similar to the F-16’s, but with important additions. Besides two traditional parameters of traditional fighters, lethality and survivability, the F-35’s specification called for sustainability in service and, in an uncharacteristic move for a top-tier warplane, affordability.
How are these goals met, and what might that mean for the future of manned aircraft in the civilian world?
Designed for simplicity
The F-35, believe it or not, was designed for simplicity. Unlike the normal sequence of engineering teams (design, manufacturability, sustainability) working in series, the F-35 teams at Lockheed-Martin and major component manufacturers like Rolls-Royce and Pratt & Whitney worked in parallel, addressing potential obstacles in real time, building a design that did not have to be frequently re-evaluated.
Danny Conroy, the U.S. program director for Lockheed Martin’s part of the F-35 project, notes that U.S. fighter aircraft average 23 years old, and that they were designed in the 1960s and ‘70s. While he did not say that 23 years of progress would be like dropping a Spad into a dogfight in the middle of WWII, the point could be taken; global opponents, realized and potential, have not been sleeping.
The F-35 is a “high-volume” fighter. While a total of 187 F22 Raptors will constitute the entire production run, some 2,400-plus F-35 variants are planned, including 680 for the Navy and Marines. With the “bargain” USAF models costing about the same as a replacement F-16, the F-35 is a reasonably priced machine, itself. As a rough performance equivalent of the F-16 (Mach 1.6 at FL 420; +-9g), and with “survivable stealth” built in, the F-35 is a rational alternative to continuing production of the non-STOVL, non-stealthy Falcon – or FA-18, which is also getting long in the tooth.
Still, with its Rolls-Royce LiftFan design, the F-35B presents a brilliant but unfamiliar new technology. Battle survivability and both field and routine maintenance had to be high on the list of priorities.
Mission Care
Without giving away secret information, Tom Hartmann, Rolls-Royce SVP Customer Business, U.S. government, acknowledges that Rolls-Royce has a Mission Care program in development. The program includes both on-condition and number-of-mission components, all designed to enhance availability.
Unusual components and systems are particular items of interest. Rolls-Royce makes the LiftFan system (Pratt & Whitney provides engines; Lockheed Martin does the airframes), and its novelty also leads to new inspection and test regimens, many of which need to be field-operational. Just how, for instance, to repair, rebalance, and test the 5-foot long, 10-inch diameter carbon drive shaft, or the (brake-technology-derived) clutch assembly at support depots – these problems have not been confronted before, but are essential to mission readiness.
Rolls-Royce’s Gregg Pyers also points out that even the overall assembly needs to be coordinated among the three big contractors; the LiftFan’s vane box is one of the first things to go into the fuselage in manufacturing. The fan itself, however, is installed some 16 months later. What happens when it needs repair, and the fighter is on an aircraft carrier?
Lessons learned
Other pieces of the aircraft demonstrate that lessons have indeed been learned. David Lawrence, who worked on the F-119 engine core, remembers a mechanic’s comment that, when a particular component was removed when the engine was in a certain orientation (and it’s not always possible to optimally orient an engine in the field!), another part would invariably drop into the works. The result of that mechanic’s comment was to design a small relief into the housing, through which a tool could be inserted, to hold the part in place long enough to support it formally.
Joel Malone, a retired Air Force colonel, now working in Business Development for Lockheed Martin, worked with other teams to simplify support. The F-16, he notes, has an APU that needs Hydrazine; the F-35 uses jet fuel, which comes from the same tanks as the engine’s supply. As a bonus, there is no LOX (liquid oxygen) requirement on the F-35.
The F-35 canopy opens from the front, presenting lower visibility surfaces for the bad guys to find and also requiring smaller actuators. It re-aligns on closing … and the pilot can see it. As is current practice, the F-35 pilot is ejected through the canopy. As crude as it is, it’s … simple.
Added concerns were made to provide access panels; there is a panel near the fuel port on the starboard nacelle that allows a laptop hookup for full-system diagnostics on the ground – using COTS electronics. Speaking of the fuel port, there is only one; when the Lightning II is full, it’s full.
Commonality is king
Across the F-35 platforms, too, commonality is king. The cockpits, weapons, avionics – all are identical, and all are as simple and available as the mission could allow. Hydraulics are backed up by a “quad-redundant” fly-by-wire system, saving weight and complexity. For example, the F-35 can fly with one horizontal tail and one rudder missing.
Some 97 percent of the F-35’s electronics are “first-tier accessible” i.e., accessible without taking other things apart; and unlike the F-15 and F-16, which have LRUs (line-replaceable units) running everything that’s connected to a wire, the F-35 saves time, money, and logistics nightmares by employing LRCs – line-replaceable cards. Only two systems on the F-35 need full LRUs.
How much of this technology will trickle into civilian aircraft – or has migrated from civilian practice to the military – is a huge topic, hampered for the moment by necessary military secrecy; but the trends across aviation – toward access; field identification, maintenance, and repair; component availability; and cost containment – are obvious, and are improving, as each new design emanates from the engineers’ computers.
For more information: www.f35.com; and
http://www.rolls-royce.com/defence/products/combat_jets/rr_liftsystem.jsp.
About the Author
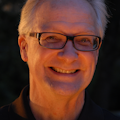
Tim Kern
Tim Kern is an aviation writer, aircraft builder, and private pilot. He is based in Anderson, IN, and can be reached at [email protected].
Tim Kern, CAM, MBA, has written for over 50 aviation publications, and is a consultant for a variety of companies; www.timkern.com.