Throughout history man has been contending with the bounds of gravity and contemplating viable means of severing it. Evidence indicates the Chinese created kites over 2,000 years ago, some capable of lifting a person and Leonardo Da Vinci conceived some ingenious but still unscientific concepts of flying machines in the 15th century. It wasn’t until the 1800s and the discovery of hydrogen gas that enabled travel by air via balloons. Much of the technology used by early would-be aviators evolved from maritime ventures and many of the old terms and principles remain in use today.
Aircraft design tools
Aircraft design over the years was based on what designers thought would work best and was then refined by adding aerodynamic enhancements or modifying the initial design to overcome shortcomings. Initial testing was accomplished in wind tunnels and the concept of the day was to build it stronger because there was uncertainty about just how strong was strong enough. Achieving the ultimate aerodynamic shape often escaped engineers resulting in something less than desired when put to the performance test. Airframe designs currently in use employ interesting contours. A “Coke Bottle” fuselage for example can reduce the whetted area resulting in a significant reduction in drag and in many cases a design that can even enhance lift. Just what makes these radical new concepts possible and how can their positive effects be predicted?
Computers provide many of the answers required to produce the ultimate aerodynamic structure. Computer-aided drafting and computer-aided manufacturing (CAD/CAM) make it possible to create an optimized construction strategy. Many manufacturers today utilize robotic production facilities where design drawings can be fed into automated machinery enabling intricate components to be produced in an efficient and repeatable fashion.
One of the better known CAD/CAM systems is CATIA (Computer Aided Three-Dimensional Interactive Application) which started as an in-house development in 1977 by French aircraft manufacturer Avions Marcel Dassault. At that time the CAD/CAM design software was used to develop Dassault's Mirage fighter jet. It was later adopted to other fighters as well as the Dassault family of business jets. It is currently used throughout the aerospace, automotive, shipbuilding, and other industries.
In 1984, the Boeing Company chose CATIA V3 as its main 3-D CAD tool, becoming the largest customer. One of the many values of this process is to eliminate the need for a design prototype. In other words, an aircraft can now proceed straight from the drawing board to production. The Boeing 777 is considered to be the first commercial airliner manufactured without a pre-production hand-built model.
Use of composite materials
Ever since the Wright Brothers built the first powered aircraft back in 1903 using mainly spruce and ash wood with a muslin cloth covering, the materials used in airplane design have been constantly evolving. Many machines today are comprised of various aluminum alloys, steel, and titanium along with other specialized metals.
Composite materials were introduced in the 1960s and have been evolving over the past 50 years. A composite by definition is an engineered material made from two or more ingredients with significantly differing properties, either physical or chemical.
Composites have two significant advantages over some of the more traditional materials: greater strength and lighter weight. A significant consideration is that the strength of a composite panel is frequently optimized based on the anticipated loads the component will experience while installed. Should a panel be subject to loads for which it is not intended, damage can result.
One of the most common forms of composite in use today is carbon fiber. It is made by heating lengths of rayon, pitch, or other types of fiber to extremely high temperatures. This heat, combined with the lack of oxygen, means that instead of combusting or burning completely, the strands turn into very thin threads of pure carbon atoms capable of being woven into sheets and mixed with hardening resins to form the components needed. In some cases carbon fiber fairings, when removed from an aircraft, need to be stored in a proper orientation. Another concern with some materials is galvanic action. Although not metal, if certain carbon fiber panels contact unprotected aluminum, corrosion can occur. Specific maintenance procedures should always be consulted when handling composite panels.
Flight control systems
One of the many notable contributions made by the Wright Brothers was controlled flight. Back then it was achieved through wing warping. Over the years flight surfaces have been moved using push rods, hydraulic actuators, and even cables and pulleys. Using cable-driven control surfaces has made a resurgence in recent years, however, the commonly used 7/19 steel braided cables have been replaced with data cables. Fly-by–wire systems enable precise and constant adjustments to maintain desired aerodynamic characteristics. Flight computers assess values from numerous sensors including control yoke or side-stick along with auto-flight systems and allow associated control surfaces to perform at maximum efficiency while keeping the aircraft flight envelope well within design criteria.
Supersonic flight
The Aerion Super Sonic Business Jet is technology in motion, although still in development, it is designed to operate efficiently within the current regulatory environment with a natural laminar flow wing achieving maximum efficiency at Mach 0.95 and Mach 1.4. Over land it will fly at Mach 0.95, creating no sonic boom, while being the fastest business jet in the world. It does have the ability to cruise at speeds up to Mach 1.2, depending on temperature and winds, without a boom reaching the ground. This is known as Mach cut-off flight and is a natural phenomenon whereby the boom essentially dissipates before reaching the ground. Mach cut-off is not dependent on new boom mitigation technology. However, to use these speeds would require onboard systems to identify maximum no-boom speed under prevailing conditions (currently in the R&D stage), and then testing the system and aircraft to ensure consistent no-boom flight above Mach 1.
Fly-by-wire will be used aboard the AS2 for all the reasons it is used on subsonic jets: precise handling, reduced workload, envelope protection, and maximum performance maneuvers when required. Aerion envisions active-control side sticks for improved crew ergonomics. Even the evolution of avionics systems from simple pressure sensitive bourdon tubes to piezo-electric components feeding high-speed digital processors enables flight crews to display more useful information in very logical formats with some systems incorporating touch screens and almost no moving parts. The fact software is used to initiate various functions, upgrades can often be accomplished without hardware or wiring changes.
Working in the Cloud
Even maintenance documentation today has succumbed to technology. Many manufacturers have already floated their publications in a cloud environment and those with proper credentials can retrieve information with many portable electronic media devices. Advisory Circular 120-78 addresses many of the challenges associated with virtual maintenance logs. The use of portable electronics coupled with aircraft connectivity systems does place an entirely new twist on supervising aircraft maintenance.
It may soon be considered an acceptable practice for a technician to oversee a maintenance action in some remote corner of the world using technology such as Skype and then issuing return to service documents to a remote printer either in the aircraft or at a nearby location. Computer hackers are now a genuine concern and Airworthiness Authorities are doing diligence to mitigate risks. Even though accessing a flight guidance or fly-by-wire system while seated in the cabin is still a long shot, the FAA is exploring controls that will make the aircraft digital firewall almost as indestructible as the metal variety.
With the constant evolution of technology it is up to the global maintenance community to make sure our members are striving to become knowledgeable on new developments and to develop the next generation aircraft technician enabling us to ensure the new fundamentals of airworthy are well understood.
Jim Sparks has been maintaining aircraft for almost 40 years with the majority of the time involving Business Aviation activities. Jim’s endeavors have placed him on six of the seven continents contending with numerous situations from routine flight dispatch to critical AOGs. His career includes maintainer, avionics/electrician, educator, tech rep, and director of aircraft maintenance. In addition to other activities he is engaged with ASTM assisting in the global development of criteria defining the Next Tech for NEXTGEN. You can reach him at [email protected].
About the Author
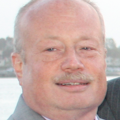
Jim Sparks
Jim Sparks has been maintaining aircraft for almost 40 years with the majority of the time involving Business Aviation activities. Jim’s endeavors have placed him on six of the seven continents contending with numerous situations from routine flight dispatch to critical AOGs. His career includes maintainer, avionics/electrician, educator, tech rep, and director of aircraft maintenance. In addition to other activities he is engaged with ASTM assisting in the global development of criteria defining the Next Tech for NEXTGEN. You can reach him at [email protected].