The Critical Role of Quality Manufacturing in Airfield Lighting
Airfield lighting ensures the safety and efficiency of aircraft operations during nighttime and adverse weather conditions, guiding pilots throughout the broad expanse of airport runways and helping them maintain correct alignment during takeoff. As an essential component of an airport’s infrastructure, it goes without saying that quality manufacturing of lights for this environment is critical as it directly impacts the lighting systems that pilots depend on for safe landings and take-offs. This article discusses what goes into the rigorous engineering and testing process of airfield lamps to ensure the products selected for this critical function are safe, reliable, perform as expected and meet both regulatory requirements and airport operator expectations.
Start with the end in mind
If we start with the end in mind, it is important to note that the FAA has specific requirements for airfield lighting to ensure the safety and efficiency of airport operations. Airfield lighting systems need to meet the specifications for intensity, color and placement, requiring a manufacturer to establish robust quality control protocols during the production process to monitor and maintain compliance for runway edge lights, taxiway lights and threshold lights. This may include testing raw materials in addition to finished products.
It is important to maintain detailed records of compliance testing, certifications and any changes made during the product's lifecycle. This documentation is crucial for audits and inspections. Important, too, is providing training for employees on compliance requirements and best practices to ensure everyone understands their role in maintaining product compliance. Finally, to ensure a product remains in compliance throughout its lifetime, a manufacturer must stay informed about changes in regulations and standards that may affect the product, so they can adjust processes and designs accordingly.
Focus on safety and reliability
It is paramount to ensure lighting products are safe to use for such a critical function. Conducting tests for electrical safety, thermal performance and compliance with safety standards can reveal potential hazards such as electrical faults, overheating or structural weaknesses that could lead to fires, electric shocks or other accidents. Evaluating the lamp’s performance under various environmental conditions needs to be part of the process to ensure the materials used can withstand harsh environmental conditions, such as extreme temperatures, moisture and UV exposure.
Rigorously testing the durability and reliability of airfield lighting to assess how the lamp holds up over time, including factors like flicker and lumen depreciation, need to be ongoing in the production process. Because these lighting systems guide pilots during landing, takeoff and taxiing, airfield lighting must operate reliably in various weather conditions and must remain functional. Hence, the lamps must withstand these conditions without fail, to reduce any risk of accidents.
Source high-quality materials
High-quality materials often perform better and last longer, reducing the need for replacements. By sourcing only high-quality materials, a manufacturer can make sure each lamp is built to withstand wear and tear. For example, using superior glass and metal alloys can significantly enhance the lamp's resistance to breakage and corrosion. The application of specialized coatings can improve the thermal and chemical resistance of the lamps, protecting them from environmental factors that could shorten their lifespan.
Responsibly sourced materials not only ensure quality, but they also contribute to sustainability. Investing in premium electrical components can lead to improved energy efficiency and lower heat generation, which are critical factors in extending the life of electric lamps. Finally, the combination of specialized manufacturing processes and high-quality materials results in lamps that typically outlast competitors' products, providing better value to airport operators.
Ensure batch-to-batch quality
Batch-to-batch quality in lamp manufacturing is crucial for several reasons. Ensuring that each batch of lamps performs consistently is vital as variations can lead to differences in brightness, color, temperature and lifespan.
By implementing these eight practices, manufacturers can make certain that each batch of lamps meets quality standards and maintains the expected reliability:
· Standardized procedures (SOP): Implement SOPs for every stage of production to maintain consistency.
· Quality control checks: Conduct regular inspections and tests on samples from each batch to verify compliance with specifications.
· Statistical process control (SPC): Utilize statistical methods to monitor and control the manufacturing process, helping to identify variations that could affect quality.
· Raw material inspection: Rigorously test and verify the quality of raw materials before they are used in production to ensure they meet predetermined standards.
· Process audits: Perform regular audits of the manufacturing process to identify areas for improvement and ensure adherence to quality standards.
· Feedback loops: Establish systems for collecting and analyzing data from previous batches to inform and improve future production runs.
· Employee training: Continuously train staff on quality standards and practices to foster a culture of quality throughout the organization.
· Traceability: Keep detailed records of each batch, including materials used, production conditions and testing results, to trace any quality issues back to their source.
By considering the above factors, manufacturers can develop airfield lighting systems that enhance safety, efficiency and reliability, ultimately contributing to smoother and safer aviation operations. Lamps from qualified manufacturers are carefully tested in a range of environments and in all aircraft applications to ensure their performance, durability and longevity. High-quality materials and precise engineering ensure that essential infrastructure—such as runways, taxiways, lighting systems and safety barriers—meets stringent safety standards and performs reliably under various conditions.
Precision engineering and quality assurance in manufacturing airfield lamps enable the production of durable, high-performance components that withstand the stresses of heavy aircraft traffic and adverse weather. This reliability minimizes downtime, reduces maintenance costs and enhances overall airport efficiency.
John Fogel, Product Manager at Amglo, has worked with the company for more than 15 years in product development, qualifying products with the FAA and building partnerships. For more information, visit www.amglo.com.
About the Author
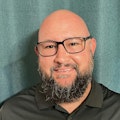
John Fogel
Halogen Product Manager
John Fogel, Product Manager at Amglo, has worked with the company for more than 15 years in product development, qualifying products with the FAA and building partnerships. For more information, visit www.amglo.com.