When the first European settlers came to North America one of the main, if not the most, significant challenges they encountered was the adaptation to a very demanding environment which in the winter season was even more challenging than what they were used to. This held true in particular for the northernmost past of the New World. That burden extended during the advent of aviation and continues today, but just about everything else in regards to how we deal with winter operations has changed.
1. Personal Protective Equipment
One of the safety devices that have improved the resilience of winter operations on the ramp over the years has been personal protective equipment (PPE). According to Steve Polak, manager of aircraft services standards and training at Jazz Aviation of Canada, good protective equipment is very important to ensure safety on the ramp during winter operations. “PPE is mandatory in our operation, quality proper fitting clothing allows our employees to remain in sub-zero temperatures for extended periods of time. Clothing must be water resistant, wind proof and able to wick moisture away from the body. A warm comfortable employee is able to focus on the task at hand” he says.
With regard to recent developments in personal protective equipment that can provide for better performance Polak says that work wear that has fully reflective surfaces replacing the need to wear a safety vest is a marked improvement. This kind of work wear provides for less bulk and a reduced chance of forgetting to don safety vests, he says.
According to Paul Schenk, manager of terminal development and activation at Greater Toronto Airports Authority, personal protective equipment, such as anti-slip boots and various types of slip on traction covers for boots, have been tested at Toronto Pearson. However, he notes, PPE should be one of the last resorts. “The first methods should be to engineer out safety concerns or put processes in place to avoid safety conflicts or possibility of injury,” he says.
2. Advanced De-Icing and Anti-Icing Equipment
When it comes to putting processes in place for performing safe winter operations, one of the things that should be noted is that de-icing and anti-icing operations can be particularly prone to cause aircraft damage because equipment operating close to aircraft always carries a risk of collision. “Our service providers have damaged aircraft while de-icing. Running prop strikes with beta truck tusks, usually the operator has deviated from SOP. With open bucket trucks we have had wing and tail strikes with the truck bucket,” says Polak.
Schenk notes that the use of sand without a proper process to ensure that it is removed in a timely fashion can lead to aircraft engine damage. “There is a lot of discussion now about the impacts to carbon fibre brake components and electrical components due to use of formiates and acetates,” he adds.
It is also out of the operational experience learnt in North America (as well as other parts of the world where winter is normally very tough, like for example the Scandinavian countries in Europe) that ground support equipment (GSE) manufacturers have been increasingly developing equipment in accordance with the principle of inherent operational risk reduction, whereby the machines are less prone to cause aircraft damage.
The principle of inherent operational risk reduction is achieving some critical mass in the manufacturing of equipment in support of winter operations with newer de-icing and anti-icing equipment being developed to reduce the likelihood of damage. Jazz Aviation’s experience has benefited from the safety features built into ground support equipment and namely the case has been that proximity sensors have helped, says Polak; he stresses, however, the tusk sensors have still struck running propellers.
Vestergaard Company, of Denmark, has also embraced risk reduction on the manufacturing side of their de-icing equipment. “Our de-icers are developed to minimize – or nearly eliminate – the risk of damage to the aircraft during operation as well as ensuring safety for both de-icing operators and other ground personnel around the aircraft," Karina Læssøe, marketing manager at Vestergaard, says. "With the long telescopic boom, the nozzle can be kept within one meter of the aircraft surface throughout de-icing operations for virtually any aircraft while still remaining at a safe distance. The length of the boom and telescope means less maneuvering around aircraft, thereby minimizing the risks of accidents.”
Læssøe highlights that a number of safety features that are engineered into Vestergaard’s de-icers, with the most prominent one being the Precision Positioning System (PPS) that helps keep the nozzle within exactly one meter from the aircraft surface, the most optimal distance in de-icing. “With the PPS, distance to the aircraft surface is maintained stable automatically thereby improving safety during operations and reducing the risk of aircraft damage,” she says.
Schenk also highlights that there have been significant improvements over the past decade in being able to specifically meter the use of anti-icing and de-icing products. “A number of companies are now providing the ability to integrate friction measuring devices and chemical application units. Using this methodology the friction measuring vehicle sends data to the chemical application trucks and tasks them where to apply material based on friction values in that area. This is of most use on runways. Essentially the truck runs the route and the chemical is automatically tasked to apply based on values sent by the friction measuring device,” he says.
3. Auditing
Winter operations have also become more resilient due to an improved oversight over the years on the suppliers of aircraft de-icing and anti-icing services, part of an industry that is rather fragmented. Regulations on air operations state that the ultimate responsibility of de-icing and anti-icing of aircraft resides with the airline operators themselves; as a consequence, the actual suppliers of these services are subject to multiple audits which can compound complexity and bureaucracy. Multiple industry initiatives are, however, aiming towards audit data sharing in order to avoid having to subject the same suppliers to multiple redundant audits.
Several international airlines establishing the IATA de-icing/anti-icing quality control pool (DAQCP) under the leadership of the International Air Transport Association (IATA) to share audit results. The program has been oriented at avoiding multiple audits of the same provider at the same location and improving the quality of inspections with fewer and more effective audits carried out by accredited DAQCP inspectors in accordance with evaluation criteria established by the pool itself. The stations are assigned each year by the pool and are based on the airports served by airline DAQCP members. The DAQCP currently consists of about 100 member airlines and through its active members, performs inspections on approximately 600 companies that provide de-icing/anti-icing services and post de-icing/anti-icing checks at more than 300 airports worldwide. The DAQCP also offers a passive membership to operators that do not have an audit organization or the experience in winter operations, according to information posted on IATA's website.
The DAQCP audits comprise multiple areas including the compliance of procedures and documentation with acceptable standards, the training and qualification of personnel, de-icing/anti-icing facilities and equipment and the integrity of sprayed de-icing/anti-icing fluids, according to information on IATA.org.
4. Real Time Data Tracking
The winter season carries the potential of paralyzing large batches of the air transport system as the media report almost invariably every year; yet the improvements in safety and effectiveness that winter operations on the ramp have witnessed over the years have historically contributed to operational discontinuities in winter. Without these improvements the air transport system would be more heavily paralyzed in winter.
The search for continuous improvement is never ending. Future incremental improvements of winter operations may be obtained by placing a stronger focus on the oversight of the actual operations concerned with the application anti-icing/de-icing chemicals on aircraft; and this result can be achieved by using systems that provide for real time data reports, thereby simplifying the operations and reducing traffic and congestion on the apron/taxiway system.
“What we have found is that by using systems that provide us real time information on where assets are, what they are doing (what chemical at what rate at what speed etc.) we are able to reduce the number of people we have trying to follow vehicles around and report on what they see rather than on real data that we are getting from the real time data tracking systems. We have put chemical tracking systems in all of our chemical application vehicles both on airside and landside. Our inspectors, especially landside, now report more on surface conditions that they see. We use the chemical tracking systems to see what is being applied and at what rates and we are able to tweak those in real time based on the results that we are seeing,” says Schenk.
“On airside we do all our own chemical applications using airport staff so the requirement for ‘oversight’ is minimized. However, the data trending for chemical usage is fantastic. It has also helped us to track the cost of chemical for each event with an eye to being able to reduce that cost going forward. I would say that the driving factors related to tracking the use of chemicals would be to improve use of products to minimize cost and improve environmental impact. Airports would also use data as to when and where and how much chemical was applied to support any issues of liability in the event of any incidents” says Schenk.
PQ:
The use of sand without a proper process to ensure that it is removed in a timely fashion can lead to aircraft engine damage.
GSE manufacturers have been increasingly developing equipment in accordance with the principle of inherent operational risk reduction, whereby the machines are less prone to cause aircraft damage.
Regulations on air operations state that the ultimate responsibility of de-icing and anti-icing of aircraft resides with the airline operators themselves.
About the Author
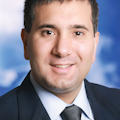
Mario Pierobon
Dr. Mario Pierobon provides solutions in the areas of documentation, training and consulting to organizations operating in safety-sensitive industries. He has conducted a doctoral research project investigating aircraft ground handling safety. He may be reached at [email protected].