How ULDs Help Distribute Pharmaceuticals Worldwide
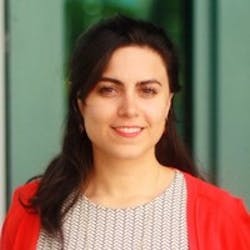
According to Vivian Berni, director of product management and strategic marketing at Sonoco ThermoSafe, the pandemic spotlighted the need for temperature control of vaccines and medicinal products.
“If a vaccine freezes or a biological product gets too warm, for example, the medicine can be ineffective and cause patient harm,” she says.
“Today, more companies across the supply chain, including pharmaceutical manufacturers, contract manufacturers and logistics partners, are addressing the requirements. This is resulting in a higher number of temperature control containers (TCCs) being used to ensure quality control of healthcare product air freight shipments,” Berni adds.
When shipping pharmaceuticals, there are several containers designed to accommodate this specialized freight.
Historically, high-value temperature-sensitive pharma goods utilized active containers to ensure temperature control in the end-to-end supply chain, Berni notes.
“Active containers are powered mechanically to heat and cool the container contents as needed, plugged in at an airport facility,” she explains.
In the past 10 years, Berni says passive technology containers have also been used more frequently.
“These do not use electrical cooling/heating, instead use special insulated materials and refrigerants that sustain temperatures for long durations,” she says.
Alternatively, hybrid containers do not use electrical or mechanical cooling, but rather insulation material that absorbs energy, which allows the system to self-charge in cooling chambers.
Berni adds that Sonoco ThermoSafe has introduced a new class of air freight containers for healthcare air freight shipments. Known as “advanced passive,” these containers combine cost-effective passive cooling technology, with an easy-to-use ULD base.
“The Pegasus ULD is the only aircraft-certified temperature control container that is a ULD,” Berni says. “This ensures it sails through airport operations smoothly, through airline ground handler operations. No nets, straps or other equipment is needed.”
Because visibility and insight into shipment performance is imperative for the pharma shipments, Sonoco Thermosafe integrated onboard telemetry into the Pegasus ULD. The technology monitors each step of the ULD’s journey as well as records and transmits data on real-time temperatures, location, door openings and other metrics.
When it comes to maintenance, pharmaceutical companies have GDP regulatory requirements to meet and high standards across all operations.
“Clear SOPs are created and audited to ensure quality control throughout multiple distribution points. Therefore, Sonoco ThermoSafe and our global airline partners hold the same high standards in our operations,” Berni says. “Every Pegasus ULD container is maintained, cleaned, quality-checked upon receipt, and when an order comes in, the unit goes through a secondary inspection on the internal and external components, as well as (an) operational check. Then the unit is pre-conditioned and ready for shipment.”
Pegasus ULDs are mostly comprised of composite material, rather than metal, which requires different repair methods.
According to Berni, the composite ULDs can be reused several times over. Any damage to the equipment can be repaired promptly by FAA- and EASA-approved ULD repair stations in its network.
“On retirement, the Pegasus is 90% recyclable because of its unique materials makeup,” Berni concludes.
About the Author
Josh Smith
Editor
Josh Smith served as editor of Ground Support Worldwide as editor from 2016 through 2024. He oversaw production of the print magazine, created GSW's newsletters on a daily basis, and updated the latest news on AviationPros.com.