Station Deicing vs. Traditional Deicing
In order to effectively deice an aircraft, there are many aspects that must be assessed. To determine the best method for an operation, gather as much information as possible and consider the following.
The Difference in Methods
Traditionally, aircraft has been deiced/anti-iced at their current parking stand after completion of ground operations, which means that all bags are loaded, all passengers are onboard and all doors are closed.
The aircraft then needs to be prepared for the deicing/anti-icing operation, ground support equipment needs to be removed and the aircraft will be configured for deicing/anti-icing operations by the flight crew. The individual parking stand needs to be big enough for deicing trucks to be able to maneuver around the aircraft and no other ground support equipment, e.g. trolleys, mobile stairs, etc., can be in the way.
It is necessary for the deicing trucks to reach all critical surfaces of the aircraft for removal of contamination and protection of the surfaces where necessary. This can be challenging at some airports due to existing infrastructure at and/or around the parking stands and growing airframes.
Station deicing is carried out at a designated remote location at the airport. This can be a centralized deicing facility or remote deicing pads. Centralized deicing facilities are typically found at airports where a continuous deicing operation is to be expected throughout the winter season.
Remote deicing pads provide maximum flexibility as to where deicing/anti-icing can take place since those pads are usually located on the way or near departure runway thresholds.
The main difference between these two deicing/anti-icing operations is that the aircraft will taxi to a deicing facility or remote deicing pad and will be treated with its engines running.
The Deicing Process
Deicing/anti-icing operation typically takes place using deicing trucks. When deicing/anti-icing operation takes place at the stand, deicing trucks with an open basket can be used, where the sprayer stands in the “bucket” during the operation and the driver operates the truck from within.
This open basket allows for the sprayer to also inspect certain surfaces by hand to check for clear ice. It enables aircraft mechanics to check engine inlets for contamination, too, and gives the sprayer the option to use a broom, cloth or something similar to remove contamination present on surfaces that should not be treated with a hot ADF spray, such as engine inlet fans, propellers and windshields.
When deicing/anti-icing operations take place with running engines, a deicing truck with an enclosed cabin must be used due to various safety reasons. The vehicle driver should not be exposed to jet blast, to noise and to exhaust fumes.
This deicing truck is operated by one person, which means that the individual inside the cabin operates the spraying boom as well as maneuver the truck around the aircraft. This is not recommended for deicing at the stand since the maneuvering space is very limited.
It is also recommended to have a team leader at each deicing pad who coordinates the trucks and has a general overview of the operation.
Current Trends
Over the last several years, deicing/anti-icing operation with running engines has gained popularity. It is preferred for several reasons:
- The airport can have its parking stands/positions available for the next inbound aircraft on time.
- The ground service provider can equip a fixed number of deicing pads with trucks, and thus have a smaller fleet while eliminating the need to drive equipment from one position to the next.
- ADF storage facilities can be located next to these deicing pads, which makes logistics easier to handle especially with just-in-time ADF deliveries to the service provider.
- The airlines can have better on-time performance since aircraft will be departing the position on time for their deicing/anti-icing treatment after off-blocks.
- The airport can have better departure management.
- Less contamination of aircraft handling positions is possible with effluent ADF.
- All involved can profit from faster operations due to:
o Easier maneuvering of the trucks around the aircraft.
o More trucks being able to treat the aircraft at the same time, thus even shorter deicing/anti-icing operation.
o Less ADF consumption due to shorter taxiing time after deicing/anti-icing operation.
Environmental Matters
What’s more, environmental issues such as ADF recovery and recycling are profitable when large amounts can be retrieved from concentrated areas such as deicing pads.
Looking at the development of glycol costs of recent years, and in regards to environmental regulations at airports, it is essential to have recovery and recycling in mind. Environmental regulations might also make it mandatory for airports to have centralized deicing operations or alternative methods to collect ADF used in deicing/anti-icing operations.
If deicing/anti-icing operations are carried out on parking stands, ADF storage needs to be accessible for deicing trucks throughout the airport premises and a decentralized ADF storage needs to be considered.
This will mean less throughput within the several ADF tank farms and might result in higher cost due to increased overall storage as well as quality control.
Advantages and Disadvantages
With departure management systems in place and accurate time stamps available for a lot of handling steps, it may become more common for airports to prefer deicing/anti-icing operations to be carried out when and where their systems calculate for the overall airport operations to be best.
The pre-planning of parking stands for incoming aircraft is easier with remote deicing areas available. This can mean that, although the aircraft is closed and ready for departure, it will not receive pushback clearance until the airport – as a whole – is able to manage this particular deicing at a certain location.
Future development towards total airport management should have more impact on planning of all ground services. Planning deicing/anti-icing operations is particularly difficult since it is mostly not to be planned for with all departures.
Restrictions regarding the possibility of deicing areas may be environmental as well as infrastructural. At some airports, the implementation of deicing areas may be restricted to certain aircraft size (e.g. max. code C) or to certain runway configurations.
Proper Training
Training and qualification of personnel plays a vital role in the success of a deicing/anti-icing operation.
If the operation is flexible regarding deicing on position and remotely, then equipment needs must be flexible. Personnel will have to be trained and qualified either for different tasks or a larger number of individuals need to be available to fulfill the different tasks needed.
Basic skills will need to be taught to every individual involved in deicing/anti-icing operations. All personnel must receive annual (recurrent) classroom training.
In addition, training for position deicing, remote deicing, spraying techniques, driving patterns, ADF handling, communication procedures, lessons learned from the previous winter season(s), etc., must be kept in mind.
The training syllabus needs to be such that individuals will be able to complete the training and quality standards will be met to ensure a safe operation.
Deicing Experience
When deciding on the deicing location, it needs to also be taken into consideration whether it can be expected that deicing personnel will be able to gain experience during the winter season.
It has been shown, that deicing operations in general increase in quality, when as much practice as possible is given throughout the season.
The use of simulators should be considered to support and increase the quality of deicing operations. Maneuvering and spraying techniques can be significantly increased by giving personnel the possibility to improve their skills throughout the winter season, for example when “waiting for snow.”
Operation Standards
Facing the rapid changes in airport operations and deicing/anti-icing operation of aircraft on the ground in the last couple of years, industry standards have been developed and maintained to cover all the various aspects of proper winter operations.
Those standards, recognized, referenced and recommended by ICAO, IATA, EASA and national authorities are reflected in approved airline winter operations programs, airport winter plans and service provider’s handling and operations programs.
Recently published global standards exist on “Aircraft Ground Deicing/Anti-icing Processes” (SAE AS6285) and “Training and Qualification Program for Deicing/Anti-icing of Aircraft on the Ground” (SAE AS6286) with more to follow shortly, e.g. on “Quality Assurance Program for Deicing/Anti-icing of Aircraft on the Ground” (AS6332).
These go together with a number of standards in recommendations, e.g. SAE AMS1424 (ADF Type I) and AMS 1428 (ADF Types II, III, and IV) on Aircraft Deicing Fluids, ARP 4902 “Design of Aircraft Deicing Facilities,” ARP 5660 “Deicing Facility Operational Procedures,” just to name some of them.
Experts from aviation regulators, organizations, airlines, airports, manufacturers and services providers from all over the globe have committed themselves to contribute and further develop those standards to ensure the safe, efficient and environmentally friendly operations of the processes that are directly related to aircraft safety during winter conditions.
About the Author
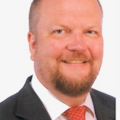
Oliver Arzt
CEO, OMAC GmbH Aviation Consulting
Oliver M. Arzt is CEO at OMAC GmbH Aviation Consulting in Germany. He also serves as co-chair on the SAE G-12 T Training & Quality Programs Committee. He can be reached at [email protected].