GPU Operation: Cable System Considerations
There is a recently installed frequency converter with a long run to the aircraft parking spot. For some aircraft everything just works but other aircraft won’t accept the power or rejects the power, and the diesel unit must be dragged out to provide the power. Everyone is upset about the downtime, lost productivity and increased costs. What is happening?
The Cable Culprits
While there is a chance that there is something wrong with the frequency converter, the more likely culprit is the cable providing the power to the aircraft. On an aircraft the voltage drops in the 400 Hz wiring are well within the allowed tolerance levels due to the short distances and lower currents. The same can not be said for the cable providing power to the entire aircraft. So what is happening at 400 Hz that makes the cable such a critical factor?
Cable Configurations
There are three basic types of aircraft power cables: three power cables and one neutral banded together every three to four feet; the same number of cables twisted together and enclosed in a scuff-resistant jacket; and six smaller power wires (typically AWG #2 for 90 kVA rated cables) twisted around a neutral wire and enclosed in a scuff-resistant jacket. All of these cables can have from 2 to 18 smaller control wires for the E&F circuit, ON/OFF pushbuttons, UP/DOWN/IN/OUT pushbuttons and for status LEDs.
In all of these cables, the number of wires in the cable, the configuration of the power wires to the neutral and to each other, as well as the size of the wires all affect the voltage presented to the aircraft from the cable plug. Per STANAG 3456, ATA 101 and MIL-STD 704F, the voltage at the external power receptacle of an aircraft must stay within 113 to 118 VAC.
Four wire banded cables are the least expensive cables and are typically used in low-power applications (< 40 kVA) where the voltage drop is lower due to lower currents. This is crucial because the inductance of the cable is different each time the cable is pulled out to an aircraft. Since the cable is only banded every three to four feet, the distance between the phase wires changes, and thus the voltage drop and the phase-to-phase voltage differs with the changing inductance. An additional disadvantage of this cable configuration is that the cables have to be replaced more frequently since they don’t have the extra insulation of a single jacket to provide scuff protection as the cable is dragged across the concrete apron to the aircraft.
Single-jacketed four-wire cables are more expensive than the banded cable, and are typically used in low- power applications up to 60 kVA. These cables have a consistent phase-to-phase voltage (though the voltage drops are different between phases since the core distance is different between phases). If the phase-to-phase voltage is critical in the aircraft being supported, then the frequency converter or voltage-drop compensation equipment must be capable of adjusting each phase voltage independently.
The standard single-jacketed six-around-one cable can support up to 90 kVA loads (this is the maximum rating for a standard aircraft power receptacle). Due to the construction of these cables, they provide the best voltage drop per foot characteristics of any aircraft cable and have the tightest phase-to-phase voltage tolerances due to the configuration of the cable. While these cables cost more to purchase, they also reduce power inconsistencies at higher loads which increases uptime and lowers maintenance costs and headaches.
Voltage Drop Compensation
Some frequency converters come equipped with an automatic voltage- drop compensation circuit. These units require separate voltage sensing wires in the aircraft cables and typically provide 7 percent to 12 percent voltage compensation. Piller frequency converters can use these wires as well, but they also have a separate capability (Intelligent-Boost) which measures the output current and the load power factor and automatically and precisely adjusts the output voltage without requiring the sense wires.
If the frequency converter in use doesn’t have the ability to automatically adjust the output voltage or it doesn’t have enough range, then voltage-drop compensation equipment should be considered. These units are used to increase the length of an aircraft cable before the voltage drop reduces the voltage to the aircraft below the allowed tolerances (typically 112 – 113 VAC).
The basic line drop compensator (LDC) consists of one or two capacitors and a transformer per phase which are used to add a fixed amount of capacitance to counteract the cable inductance at a specific load, cable type and length. The transformer usually has between seven and 10 taps that are used to adjust the percent of capacitance that is added to the line. An LDC is setup using a resistive and reactive load bank that are typically set to the maximum load that is expected to be supported with the aircraft cable. The major problem for this type of device is that the capacitance is fixed for a specific inductance and power factor. If either of these changes significantly, then the applied capacitance could result in an out of tolerance voltage condition at the aircraft receptacle.
The line voltage regulator (LVR) was developed by Piller to provide varying amounts of capacitance based on the actual current and voltage being supplied to the aircraft. This device can maintain the aircraft receptacle phase-to-phase and phase-to-neutral voltages to within +/- 1.5 volts at any load. Thus, a boarding gate or maintenance area that is equipped with an LVR can handle any aircraft or load without requiring any tuning after the initial setup.
Conclusion
When it is determined that there is a voltage-drop problem, there are several options to try in order to solve the problem. Shortening the cable will lower the voltage drop, especially for higher current loads. If using banded cable, try replacing it with a seven-conductor single-jacketed cable to reduce voltage variations and voltage drops for a given length. If the shortest, single-jacketed cable that is adequate for the aircraft spot is already being used, then consider adding an LDC or LVR to the circuit.
For more information on this subject, download the “Cable Design for 400 Hz networks” at www.piller.com.
About the Author
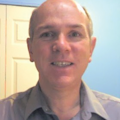
Mark Frink
Mark Frink is sales engineer for Hobart Ground Power - ITW GSE Group. He is responsible for engineering support to the company's sales force and customers of utility and diesel-powered PCA units, 400 Hz frequency converters and 28V DC power supplies.