How to Plan Passenger Boarding Bridge Maintenance and Inspections
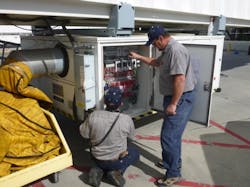
Passenger boarding bridges (PBB) are an essential component of airport infrastructure that connects airport terminals to aircraft. They provide a safe and convenient means for passengers to board and disembark from aircraft, while also facilitating the loading and unloading of cargo and luggage. To ensure the safety of passengers and airport personnel, it is essential that passenger boarding bridges are regularly inspected and maintained.
PBB inspection comes involves different procedures and focuses. We break down some of the common inspections, their purpose and frequency.
Purpose of PBB Inspections
PBB inspections are designed to identify any defects, damage or wear and tear that could compromise the safety of passengers or airport personnel. These inspections are carried out to ensure that the bridges are functioning correctly and comply with the safety standards and regulations set out by national and international aviation authorities.
PBB inspections are necessary to ensure the longevity of the equipment. Regular inspections help to identify any issues early on, which can then be addressed before they become more severe and costly to repair.
Frequency of Inspections
The frequency of PBB inspections varies depending on the type of inspection and the airport's operational needs. It’s recommended inspections are conducted at least once a year, as a minimum requirement. More frequent inspections may be required in some cases, such as in harsh weather conditions or areas with high levels of pollution.
Regular visual inspections of PBBs are conducted daily by airport personnel. These inspections are essential in identifying any visible damage or defects, such as cracks or loose bolts. Any issues identified during daily inspections should be reported and addressed immediately to prevent further damage and ensure the safety of passengers and airport personnel.
JBT Vice President of Sales John Thompson says preventive maintenance should be completed per the requirements outlined in a maintenance manual. The specific scope of work requirements for each of the scheduled preventive maintenance inspections are identified in the annual, semi-annual, and quarterly preventive maintenance instructions.
A preventive maintenance program needs to be scheduled by an airport’s maintenance project manager, who will coordinate with airport operations to schedule PBB equipment to be out of service for the duration required for each specific maintenance check. In most cases the duration of the maintenance for each PBB will be as follows:
· 1st Quarter Inspection: 2 People 8 Hours
· 2nd Quarter Semi-Annual Inspection: 2 People 12 Hours
· Semi-Annual Power Wash: 2 People 8 Hours
· 3rd Quarter Inspection: 2 People 8 Hours
· 4th Quarter Inspection Annual Inspection: 2 People 12 Hours
· Annual Power Wash/Touch-Up Painting: 2 People 12 Hours
Types of Inspections
There are different types of inspections that are conducted on passenger boarding bridges, each with its specific purpose and scope. Thompson says it’s important Lubrication of the PBB and Visual Inspections for key things out of place are key during the inspection process.
Visual Inspection
Visual inspections are the most basic type of inspection and are conducted to identify any visible damage or defects. This inspection is usually carried out daily by airport personnel, who check for any signs of wear and tear, corrosion, or loose bolts. Any issues identified during this inspection should be reported and addressed immediately to prevent further damage and ensure the safety of passengers and airport personnel.
Thompson says look for things out of place, damaged, worn and safety hazards. Also listen for binding and popping during operations.
Functional Inspection
Functional inspections are conducted to ensure that the passenger boarding bridge is operating correctly and safely. This inspection is usually carried out at least once a year and involves testing all the mechanical and electrical components of the bridge, such as the hydraulic system, the passenger tunnel and the lighting system. Any issues identified during this inspection should be addressed immediately to prevent further damage and ensure the safety of passengers and airport personnel.
Thompson says it’s important to include wheels, racking, canopy closure for NFPA 415 issues and rails for roller issues in this inspection.
Ultrasonic Testing
Ultrasonic testing is conducted to identify any hidden defects or cracks in the metal components of the passenger boarding bridge. This inspection is usually conducted every five years and involves using ultrasonic equipment to detect any hidden defects or cracks in the metal components. Any issues identified during this inspection should be addressed immediately to prevent further damage and ensure the safety of passengers and airport personnel.
Thompsons says ultrasonic testing could come into play depending on location and environment for the PBB. It has to be an extreme corrosive environment to use Ultrasonic testing as most places in the U.S. excluding Hawaii wouldn’t warrant the need during the 20–25 years life span.
About the Author
Joe Petrie
Editor & Chief
Joe Petrie is the Editorial Director for the Endeavor Aviation Group.
Joe has spent the past 20 years writing about the most cutting-edge topics related to transportation and policy in a variety of sectors with an emphasis on transportation issues for the past 15 years.
Contact: Joe Petrie
Editor & Chief | Airport Business
+1-920-568-8399
>> To download the AviationPros media kits, visit: Marketing Resource Center
>>Check out our aviation magazines: Ground Support Worldwide | Airport Business | Aircraft Maintenance Technology