The COVID-19 pandemic has literally halted the world. The latest estimates indicate that the possible impact on world scheduled passenger traffic compared to baseline (business as usual) would be approximately $343 to $383 billion for the 2020 year (ICAO, 2020), with about 25 million jobs at risk (IATA, 2020). We are unlikely to see a return to 2019 passenger volumes before 2023-2024 (A4A, 2020). Revenues will take even longer to recover. Air travel took three years to recover from 9/11 and 7-plus years from the global financial crisis. Air cargo took 10 years to recover post the global financial crisis. COVID-19 has forced several airlines across the globe to restructure or cease operations. The world economy is projected to shrink nearly 4% in 2020. People will be reluctant to travel or even book travel — until there is a strong degree of confidence that the health crisis and associated risks are behind us.
The pandemic is a significant source of anxiety, stress and uncertainty for almost everyone. Among the magnitude of airline industry challenges is the importance of protecting worker health during the current pandemic. That includes individual well-being (physical health/protection, mental health), community level support (e.g., peer support, coping with family situations such as childcare and distance learning) and organizational level support of the staff well-being.
Personal Protective Equipment (PPE) is equipment that protects the user against health or safety risks at work. Despite engineering controls and safety systems in place, some hazards might remain, and consequently, could cause injuries to the lungs, the head and feet, the eyes, the skin and the body. Common PPE can include items such as a safety helmet, gloves, respiratory protective equipment, eye protection, hearing protection, high-visibility clothing, safety footwear and a safety harness. Individuals must be trained to know at least the following: when PPE is necessary, what PPE is necessary, how to properly put on, take off, adjust and wear the PPE, the limitations of the PPE and proper care, maintenance, useful life and disposal of PPE. PPE keeps Aircraft Maintenance Technicians (AMTs) safe and healthy as aircraft maintenance and repair poses many challenges and include exposure to numerous hazards. PPE varies with the job and task. For example, safety glasses, a face shield and goggles protect your face and eyes, depending on the task and materials.
The COVID-19 pandemic has brought new challenges to PPE use in aircraft maintenance operations. First, AMTs need to be protected from coronavirus using certain protection such as face masks or coverings and disposable gloves. Secondly, using these may interfere with other PPE (e.g., fogging up the safety glasses) or cause communication difficulty (e.g., sound will be muffled, facial expressions will be concealed). Thirdly, there is a strict requirement for cleaning/disinfect re-usable PPE and sharable items such as fall protection PPE.
Protecting Employees & Operators at Boeing
To protect maintenance technicians who work on Boeing aircraft, some maintenance procedures were enhanced to ensure the safety and health of technicians from airborne contaminates while performing tasks. For example, AMM procedure for removing and installing Recirculation Air Filters across Boeing models now requires hooded disposable coveralls, non-vented safety goggles and N95/99/100 respirator in addition to disposable safety gloves. Once removed, the old filter needs to be immediately placed in a plastic bag and tape sealed. The technicians will disinfect the plenum before installing the new filter. All tools used for filter replacement must be disinfected. Upon completion of the task, PPE needs to be tape sealed in a bag. The bags with old filter and PPE need to be discarded per airline, local health, safety and regulatory procedures.
Face coverings are required at all Boeing facilities in the US. Per CDC guidance, cloth face coverings should fit snuggly but comfortably against the side of the face. It should fully cover both the nose and mouth and be secured with ties or ear loops. The face covering should allow for breathing without restriction and can be washed and machine dried without damage or change to its shape. Cloth face coverings should not be worn near an open flame (e.g., during welding). Conventional face coverings turned out to pose a big challenge for deaf and hard-of-hearing employees because seeing someone’s face is essential for them to understand co-workers and conduct business. Facial expressions are extremely important for communication and deaf and hard-of-hearing employees who do not use sign language rely on hearing aids and lip reading to communicate with others. Facial expressions are equally necessary for those who communicate using American Sign Language (ASL), as the word could mean something completely different without specific facial expressions in ASL. After some employees spoke up about the issue, Boeing leadership took a One Boeing approach to provide health complied, clear face coverings that allow deaf or hard-of-hearing employees visibility to see coworkers’ faces for lip reading.
Correct/Appropriate Usage
The Center for Disease Control (CDC) provides instruction on how to correctly wear face coverings (https://www.cdc.gov/coronavirus/2019-ncov/prevent-getting-sick/how-to-wear-cloth-face-coverings.html). When removing face coverings, individuals should not touch their eyes, nose or mouth. Individuals should store face coverings in a paper bag or hang in a personal space and wash hands immediately afterwards.
Some personal masks are equipped with exhalation valves. These valves may present a risk for others around you. Individuals need to follow specific guidance by their own organizations regarding masks with exhalation valves and elastomeric Air Purifying Respirators (APRs). For example, at Boeing sites, individuals must cover the entire valve with a procedural mask. Use of an APR at Boeing is limited to production processes and hazardous work where specifically required or recommended. Employees are not allowed to bring an APR from home to use it at work because Boeing cannot verify these respirators meet requirements for use (e.g., filter, medical qualification, fit testing and training).
PPE such as nitrile and latex gloves are commonly used during the COVID-19 pandemic. However, they do not take the place of task-specific gloves, such as cut resistant gloves or specific gloves designated as PPE when handling chemicals. Some companies have selected task-specific gloves coated with nitrile or latex rubber for handling materials in order to reduce the spread of COVID-19 in addition to hand protection. Please note coated gloves are not a substitute for chemical gloves.
To properly and safely remove disposable PPE gloves, individuals should use a process (see Illustration 1) to avoid contaminating hands, or snapping the gloves to cause spray. Individuals should dispose gloves in regular waste bins or hazardous waste disposals when required. Wearing gloves does not substitute for cleaning hands since hands can get contaminated while wearing or removing gloves. Individuals should wash their hands immediately after removing and disposing gloves.
Shared IT equipment (keyboard, mouse and other hard touch points) should be cleaned and disinfected with 70% isopropyl alcohol (IPA) or 99% IPA or Mark E II disinfectant, germicidal detergent. Only 70% IPA can be used on touch screens or tablets. When 70% IPA is unavailable, wear gloves during the touchscreen use.
Correct Cleaning & Disinfection
The CDC recommends that cloth face covering should be routinely washed depending on the frequency of use, for example, daily cleaning for daily use. It is helpful to have more than one face covering to rotate use between cleaning. Face covering should be replaced when it becomes damaged or worn.
Reusable gloves, including task-specific gloves, must be cleaned frequently. They can be washed and allowed to dry for re-use. It is recommended to provide multiple pairs of task-specific gloves to employees to allow cycle use of different gloves throughout the day, or change when the gloves are damaged or compromised.
Exoskeletons, or external wearable devices used to increase mechanical leverage, strength or speed, were initially used in military and medical rehabilitation applications. Boeing Research & Technology researchers introduced industrial exoskeletons to the manufacturing environment in 2017 to help technicians, electricians and painters work more safely. For example, the exovest, a type of exoskeleton, is worn on the upper body like a backpack. A switch activates a system of springs that supports the arms and neck. It feels as though it is gently holding the user’s arms up in the air, freeing the hands to do work with ease. To mitigate COVID-19 hazards when using exoskeleton technologies, Boeing requires exoskeleton wearers and those working in close proximity to the wearers must use PPE, including procedural masks and disposable gloves. All exoskeletons must be disinfected before and after use. The preferred method is using 70% IPA to disinfect the entire exoskeleton, especially the high-touch areas such as padding, straps or handles.
While performing maintenance on aircraft, AMTs frequently work on the top of airplanes’ fuselages and wings. While on top of aircraft, AMTs are high enough to be at risk of serious injury in the event of a fall to a lower level. Occupational Safety and Health Administration (OSHA) requires fall protection for more than four feet. To protect workers on elevated surfaces, many maintenance and hangar facilities provide fall arrest systems that workers connect to while they work. Manufacturers of fall protection PPE have specific cleaning requirements to ensure the safety and integrity of the webbing and metal components. Harsh chemicals or abrasive cleaners (e.g., bleach) can damage the fibers and weaken the components. Fall protection PPE users should use disposable gloves. High touch areas (e.g., snap hooks, karabiners or permanentl- mounted overhead self-retracting lifelines) can be disinfected with alcohol based cleaners.
In conclusion, PPE offers protection to AMTs during the COVID-19 pandemic. Correct use and cleaning/disinfecting will ensure its effectiveness in keeping AMTs safe and healthy. Unique challenges introduced by additional PPE in aircraft maintenance can be managed through collaborative problem solving with end users and some practical tips.
References:
Airlines for America. (2020). Tracking the Impacts of COVID-19. https://www.airlines.org/wp-content/uploads/2020/03/A4A-COVID-Impact-Updates-72.pdf
International Air Transport Association (2020). 25 Million Jobs at Risk with Airline Shutdown. https://www.iata.org/en/pressroom/pr/2020-04-07-02/
International Civil Aviation Organization (2020). Effects of Novel Coronavirus (COVID-19) on Civil Aviation: Economic Impact Analysis. https://www.icao.int/sustainability/Documents/COVID-19/ICAO_Coronavirus_Econ_Impact.pdfb
McGill, A. (2019, February 26). Exoskeleton technology is getting a trial run at Boeing to make workers’ jobs less strenuous. https://www.live5news.com/2019/02/26/exoskeleton-technology-is-getting-trial-run-boeing-make-workers-jobs-less-strenuous/
Dr. Maggie Ma is an Associate Technical Fellow who specializes in maintenance human factors at the Boeing Company.PPE User Tips
Wearing face masks and cloth covering directs exhaled air upwards where it contacts protective eyewear lenses. Warm water condensing on the cooler surface of the lens creates fogging, which decreases vision and creates discomfort. To prevent fogging due to face covering, there are several methods: (1) Use protective enhanced eyewear with a seal/contact at the bottom of the glasses. (2) Wash the glasses with soaping water and shake off the excess water. Let the glasses air dry or gently dry off using a soft tissue before putting them back on. (3) Fold a tissue into a thick rectangle and layer it to the inside of your mask, where it lies atop the bridge of your nose. This helps absorbs the moisture from your breath. (4) The edges of a face mask should always fits snugly and cover all of your nose and mouth. If the top of your mask fits loosely, simply fold down the top fourth of the mask before putting it on.
About the Author
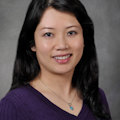
Maggie J. Ma
Associate Technical Fellow, Boeing
Maggie Ma is a Certified Human Factors Professional (CHFP) who specializes in maintenance human factors, and a Boeing Technical Fellow. Maggie received her Ph.D. in Industrial Engineering/Human Factors Engineering in 2005 from State University of New York at Buffalo. Maggie has 20 years of experience in conducting applied human factors research to improve aviation safety through developing various safety programs (e.g., event investigation, training, self-reporting, and observation of normal operations). She has authored over 70 technical publications, has chaired technical sessions, and is frequently a speaker at aviation safety conferences and workshops. She has worked closely with airlines, manufacturers, maintenance organizations, ground service providers, and regulatory agencies around the world.
Maggie joined the Boeing Company in January 2012. Her primary responsibilities include providing implementation support to customer airlines, maintenance organizations, and internal customers on a wide array of safety processes/programs, e.g., the Maintenance Event Decision Aid (MEDA) process, the Ramp Event Decision Aid process, Maintenance Human Factors training, a Safety Management System, Maintenance Line Operations Safety Assessment (LOSA), and Ramp LOSA. She also leads several Boeing initiatives and innovation projects. Maggie and her former lead, Dr. Bill Rankin received the Engineering Team of the Year Award for Boeing Commercial Aviation Services in February 2013. Maggie received the Boeing Service Culture Excellence Award in June 2018.
Previously, Maggie was a faculty member of Aviation Science at Saint Louis University and also worked as a senior usability consultant at Perficient Inc. She was an Amelia Earhart Fellow 2004-05.
Education
- Bachelor of Science (1999), Engineering Management, Beijing University of Technology.
- Master of Science (2002), Industrial Engineering/ Human Factors Engineering, SUNY-Buffalo.
- Ph.D. (2005), Industrial Engineering/ Human Factors Engineering, SUNY-Buffalo.
- Certificate (2019), Psychology of Leadership, Cornell University.
Professional Affiliation
- Human Factors and Ergonomics Society (HFES)
- Board of Certification in Professional Ergonomics: certified Human Factors Professional (CHFP)
- Boeing Community of Excellence in Human Engineering
- International Civil Aviation Organization (ICAO) Human Performance Task Force
- European Union Aviation Safety Agency (EASA) Human Factors Collaborative Analysis Group (HF CAG)
- FAA’s Research, Engineering, and Development Human Factors Subcommittee
- Airlines for America (A4A) Maintenance Safety Committee
- UK Royal Aeronautical Society Human Factors Group: Engineering (RAeS HFG:E) (corresponding member)